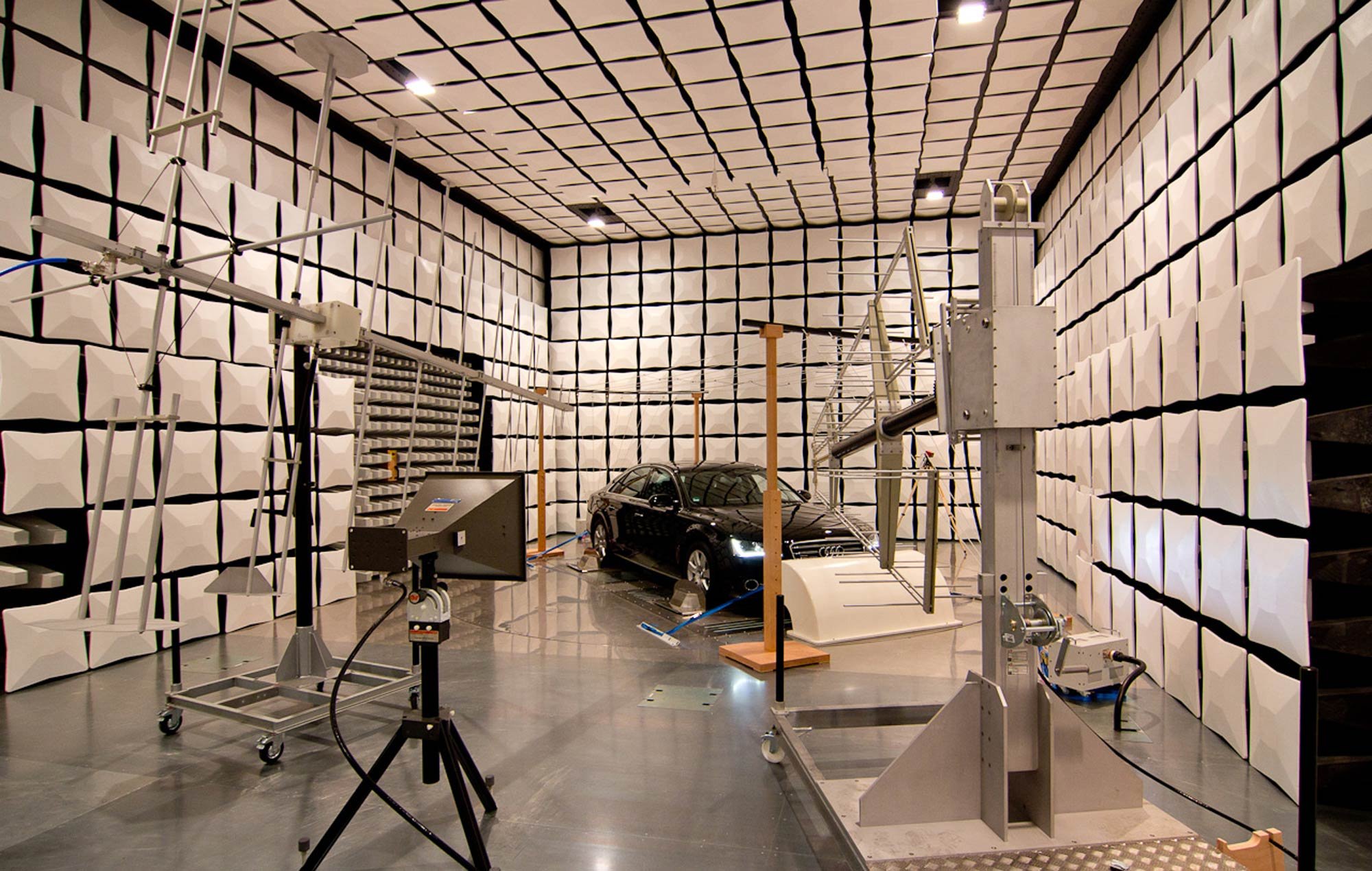
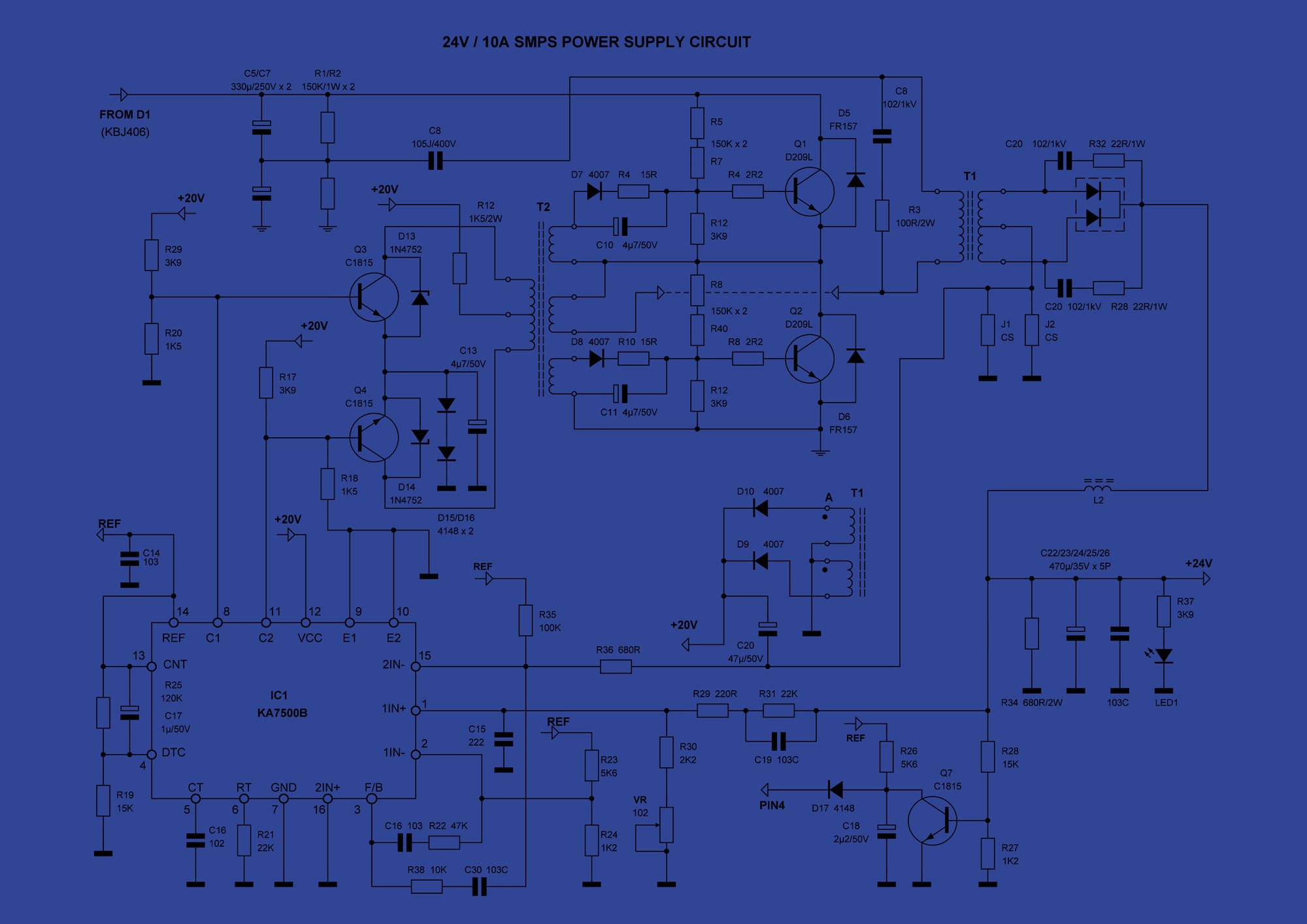
Start Here:
MIL-HDBK-235: “Military Operational Electromagnetic Environmental Profiles”
MIL-HDBK-235 helps procuring agencies define electromagnetic environments for military and aerospace contracts.
MIL-HDBK-235 attempts to provide guidance for people trying to figure out the operational electromagnetic environment (EME) for a particular platform/program, as per MIL-STD-464 Section 5.3. (You can freely download MIL-HDBK-235 here.) If you read the appendices for that section of 464 (Always Read the Appendices!), you’ll find MIL-HDBK-235 called out several times for information and procedures on how to establish appropriate EME levels for a program. This will feel especially important, since the EME tables contained in the main text of 464 Section 5.3 contain some terrifying numbers–if you’re used to testing space hardware to 20 V/m, 464 Table III will tell you about multiple frequency ranges where both the peak and average field strength values are well above 150 V/m. So you follow the guidance of the appendix and turn to MIL-HDBK-235.
The problem is that MIL-HDBK-235 is a document with multiple parts, and every part except 235-1 (current rev: 1D, 2018) is classified. Below is the table listing the other document parts–the (U) next to each title just means that the title is unclassified, but the document as a whole is still inaccessible (which can feel a little soul-crushing when you just thought you’d found that answer to your problems, to be honest).
More than anything else, MIL-HDBK-235 is a guidance document for procurement agencies. The ones who need it will have access to the classified portions and can use them to set their EMEs appropriately. They can then spec the programs to the correct environments (although as 464 points out, those environments are often fluid–for instance if a unit that was designed to go in a terrestrial vehicle is redeployed on a naval vessel). Once the procuring agency sets those levels, the program can then do analyses to flow the requirements down to a MIL-STD-461 test level for different modules or equipment.
MIL-HDBK-235-1 has some helpful information about the general factors that go into the levels found in the classified portions of the document, as well as information about how to use that data. It also has guidance for doing average vs. peak power calculations, and deriving power density in the near and far fields for different types of antennas. What it does NOT do is tell you how to go from the External EMEs found either in its classified portions or the public tables of MIL-STD-464 Section 5.3 to MIL-STD-461 RS103 test levels. Simulations can be very helpful in doing that tailoring, taking into account the physical geometry of the platform, including the shielding effectiveness of different areas, and estimating how much field strength might be expected to develop in different regions when the whole platform is illuminated by plane waves with characteristics derived from MIL-HDBK-235 or similar documents.
TIP:
For those working in space applications, there is a NASA Johnson Space Center document, JSC-CR-06-070 “Space Vehicle RF Environments”, dating to 2018, that is publicly available.It has content very much like what is in classified sections of MIL-HDBK-235, but with no reference to sources. It includes some fascinating data surveying the EME of different orbits and at different times.
BCI Testing: MIL-STD-461 CS114, RTCA DO160 Sec 20, and ISO 11452-4
Bulk Current Injection (BCI) testing is one of the best ways to ensure that operations will not be interrupted by low frequency noise via either radiated or crosstalk mechanisms of interference.
All Bulk Current Injection (BCI) tests are addressing the same risk: given a relatively long cable run mounted relatively close to conductive structure (vehicle chassis), the cabling can pick up electromagnetic noise from the surrounding environment. Cabling is especially good at doing this at lower frequencies, below 200-ish MHz. Various sources can be: crosstalk from co-routed cabling, noise from on-board RF transmitters, or noise from the external environment (radars, comms, HIRF, etc.). At higher frequencies, the risk is addressed by testing radiated susceptibility/immunity (e.g. RS103) in a semi-anechoic or reverb chamber. However there are drawbacks to that approach at lower frequencies: the longer distances of radiated testing doesn’t represent the crosstalk risk; reverb chambers are harder to spec at lower frequencies; radiated testing at 1 m is in the near field at lower frequencies, which can lead to a lack of replicability. Additionally, BCI testing can be done in a shield room instead of a more specialized (and often harder to schedule) ALSE or reverb chamber.
Thus BCI testing, where current is directly induced in the cable under test (CUT), is generally preferable below 200 MHz. There are three comparable standards that do this for defense, aerospace, and automotive industries that are worth examining:
MIL-STD-461G, CS114 (Defense and aerospace)
RTCA DO160, Section 20 (Civilian aircraft)
ISO 11452-4 (Automotive)
Differences between the three can be seen immediately from their frequency ranges and maximum induced current levels:
CS114: 10 kHz - 200 MHz, up to 109 dBuA
DO160: 10 kHz - 400 MHz, up to 109 dBuA
ISO 11452-4: 1 MHz - 400 MHz, up to 100 dBuA
DO160 mentions specifically that their frequency range is meant to overlap with their radiated susceptibility testing range, which starts at 100 MHz. ISO, focused on the automotive industry, doesn’t have as many strong threats in the kHz range (although given the increasing prevalence of HV systems in EVs switching in the kHz range, I wonder if this will change in the future).
Another thing to compare is the maximum amplitudes. MIL-STD-461G has a good rule of thumb that for wiring suspended 5 cm above a ground plane (as is specified in all the test testups), an incident E-field of 1 V/m will result in 1.5 mA of induced current. CS114 and DO160 have maximum levels of 109 dBuA, equivalent to 300 mA and assuming a maximum threat of 200 V/m. In both cases, HIRF (high intensity radiated field) is one of the driving concerns. If we apply the same formula to ISO 11452-4, we get an incident field of 67 V/m. This is a bit odd because the maximum vehicle level radiated immunity test in this frequency range goes up to 100 V/m, but there may be a presumption that the vehicle chassis provides some level of shielding to the unit.
The other thing to consider is the modulation of the injected current and the dwell times. All methods recommend dwelling for the response time of the unit under test (UUT) but have different minimums:
CS114: Amplitude modulated (AM) only, dwell time 3 sec
DO160: Both AM and continuous wave (CW), dwell time 1 sec
ISO 11452-4: Both AM and CW, dwell time 1 sec
Generally speaking a unit tested to DO160 BCI would be considered equivalent to one tested to CS114, but the different dwell times means there’s a small chance the DO160 test could miss something, while the fact that CS114 doesn’t cover 200 - 400 MHz means there’s a small chance something could be missed there.
In other respects, the test setups between the three are generally identical. They all have cables suspended 5 cm above a ground plane, with a monitor probe in addition to the injection probe during testing. They test cable bundles per connector, and if it is known that chassis will be used for current return the ground lead is excluded from the cable bundle. For CS114 and DO160, if there are cables with redundant purposes they should all be subjected to the BCI stimulus simultaneously; this situation generally does not arise on automotive modules.
TIP:
To save time and hassle later, test all cables unshielded but have a shielded version ready to swap in if there’s a serious failure. Especially on aerospace projects it is not uncommon to spec that all cables will be shielded and to do EMC testing that way–then later in the project to ditch the shielding for cost/weight purposes, rendering the earlier EMC testing meaningless. Testing without shielding gives you good confidence that the unit will be OK if shields are removed, or it will give you hard data to show that shields are necessary.
TIP:
GSFC-STD-7000b (as usual) has some excellent additional information on this test method in Section 2.5.3.3.6, which expands on some fundamental aspects beyond what you’ll find in the MIL-STD-461 appendices.
ESD: IEC 61000-4-2, MIL-STD-461 CS118, ISO 10605, et. al.
Several standards cover ESD testing in similar ways. This article gives an overview plus places to look for additional guidance and alternate discharge models.
The basis for most ESD (electrostatic discharge) tests comes from IEC 61000-4-2, “Testing and measurement techniques–Electrostatic discharge immunity test”. The active 2008 version can be purchased here, with a new version expected in 2025. ISO 10605, “Road vehicles — Test methods for electrical disturbances from electrostatic discharge” (purchase 2023 version here) adopted the test method for the automotive industry. MIL-STD-461 included ESD testing for the first time with Rev G (freely available here) with the CS118 test method–and it looked pretty familiar. See comparisons below.
TIP:
If you have questions about ISO10605 or IEC 61000-4-2, you can see if there are answers in the freely available MIL-STD-461G CS118 or related appendix (Section A.5.16) before purchasing from IEC or ISO.
Testing is specified for units that are powered off (representing the danger from discharge when being handled or installed) and when turned on (representing threats present in its operating environment). They also include air and contact discharge, with air discharge generally being more severe. Contact discharge is mating two conductive objects at different potentials together and seeing the surge of charge transfer. Air discharge is when you reach for a metal doorknob on a dry/cold day and feel an actual spark just before you touch the door. Maximum testing voltages should be adjusted based on the expected operating conditions (how often humans interact with the unit, if it is installed in a humidity-controlled environment, etc.).
TIP:
ANSI C63.16, “Guide for Electrostatic Discharge Test Methodologies and Acceptance Criteria for Electronic Equipment”, is an available guidance document for ESD testing (the 2016 version is available for purchase here; a new version has been drafted and is currently going through ANSI approvals). It gives additional context
Almost all ESD test standards and commercially available ESD test guns/simulators base their waveforms off the human body model (HBM). The CS118 version is below.
However, there are cases where the main threat does not come from human interaction. Generally speaking the industries have determined that testing based on the HBM is adequate to identify most hardware weaknesses to ESD (although the ANSI C63.16 working group will tell that’s definitely not 100% true). I was once looking into a case where the main threat to a satellite orbiting in Low Earth Orbit was definitely going to be spacecraft charging, and did some research to see if there were other standard models available.
TIP:
The only one I was able to find was from an outdated military standard, MIL-STD-1541A (1987) (freely available here). You can see an alternate discharge model below, and the document has information about ways to vary different parts of the circuit to address different threat waveforms.
MIL-STD-331D (download here) includes circuit values for helicopter-based discharges for fuzing systems and ignition protection devices as well, to be inserted into a more traditional IEC 61000-4-2 circuit setup. Appendix A.5.8.3.2 of MIL-STD-464D also has information on helicopter-borne discharges & ordnance.
MIL-STD-464: “Electromagnetic Environmental Effects Requirements for Systems”
MIL-STD-464 is the main aerospace/defense document that applies E3 requirements to full systems and platforms.
MIL-STD-464 is an interesting beast, less well known than its counterpart MIL-STD-461. MIL-STD-464 is currently on Rev D and can be officially downloaded for free.
This document is concerned with making sure full systems (aircraft, tanks, etc.) are able to operate safely in regards to all the potential threats from the electromagnetic environment. Testing to MIL-STD-461 is part of making sure that a given component will integrate safely with the larger platform, ensuring electromagnetic compatibility. However, the broader MIL-STD-464 standard has many additional concerns: making sure aircraft are safe when hit by lightning; making sure space RF systems don’t suffer from multipaction; controlling intermodulation products from RF systems installed on naval vessels; making sure that personnel and ordnance isn’t affected by the excess charge picked up by aircraft in flight, and much more. It includes sections on lightning, EMP, RADHAZ, TEMPEST, ESD and several others. So while it is one of the primary sources of EMC requirements on defense and aerospace projects, it encompasses a much broader universe of E3 (electromagnetic environmental effects).
TIP:
As with MIL-STD-461, anyone who takes the extra time to read the appendices will be amply rewarded with context, lessons learned, and additional technical details.
TIP:
It was frustrating to me for a long time that MIL-STD-464 requires testing as verification for Multipaction (relevant to space RF systems), but did not give any hints or pointers to a test standard. AIAA-S-121 does include such a reference, to ECSS-E-20-01A, Space Engineering – Multipaction and Test, European Space Agency (ESA) for the European Cooperation for Space Standardization (ECSS), 5 May 2003.”
TIP:
SMC-S-008 is a good tailoring of all of MIL-STD-464 for defense satellite and launch vehicle applications. This includes multipaction, as I complained about above, lightning, and other EME concerns (not just EMC, as MIL-STD-461 addresses). It is freely publicly available, unlike AIAA-S-121.
MIL-STD-461: “Requirements for the Control of Electromagnetic Interference Characteristics of Subsystems and Equipment”
MIL-STD-461 is one of the core EMC standards, having evolved with military applications since WWII. It is widely used in the aerospace and defense sectors.
MIL-STD-461 is a landmark document in the world of EMC standards, and there are a lot of other standards that derive from this one. The easiest place to find a copy of MIL-STD-461 (free, as most government standards are) is here, or the official site is here. The current edition is Rev G, and the working group for the standard is currently drafting Rev H.
MIL-STD-461 is more of a document that specifies test methods than a strict requirements document, and while it has suggested limits for many of the tests, in most cases those limits should be tailored. For general aerospace and defense projects MIL-STD-464 is the actual requirements document, and the tests in MIL-STD-461 are how you document compliance to the EMC requirements.
TIP:
Tailor, tailor, tailor! Beware of any project that simply tells you to “meet 461”--even accepting 461 as the overarching requirement, tailoring 461 is key for saving testing time and budget and not wasting resources designing to inappropriate or inapplicable requirements. I’ll discuss this more in articles dedicated to each test method.
TIP:
Read the appendices! More than most standards, the committee behind MIL-STD-461 documents background information for every section of the main document. This includes context, lessons learned, and why different changes have been made over time. There’s a wealth of information in there.
TIP:
MIL-STD-461 does not have a requirement to perform testing in a certified lab. While many of the labs that have the equipment needed to perform 461 testing are certified (to ISO, by ANLAB or A2LA, etc), that is not required. Testing in an uncertified lab or your own facility is allowed as long as you can meet the test equipment and test reporting requirements.