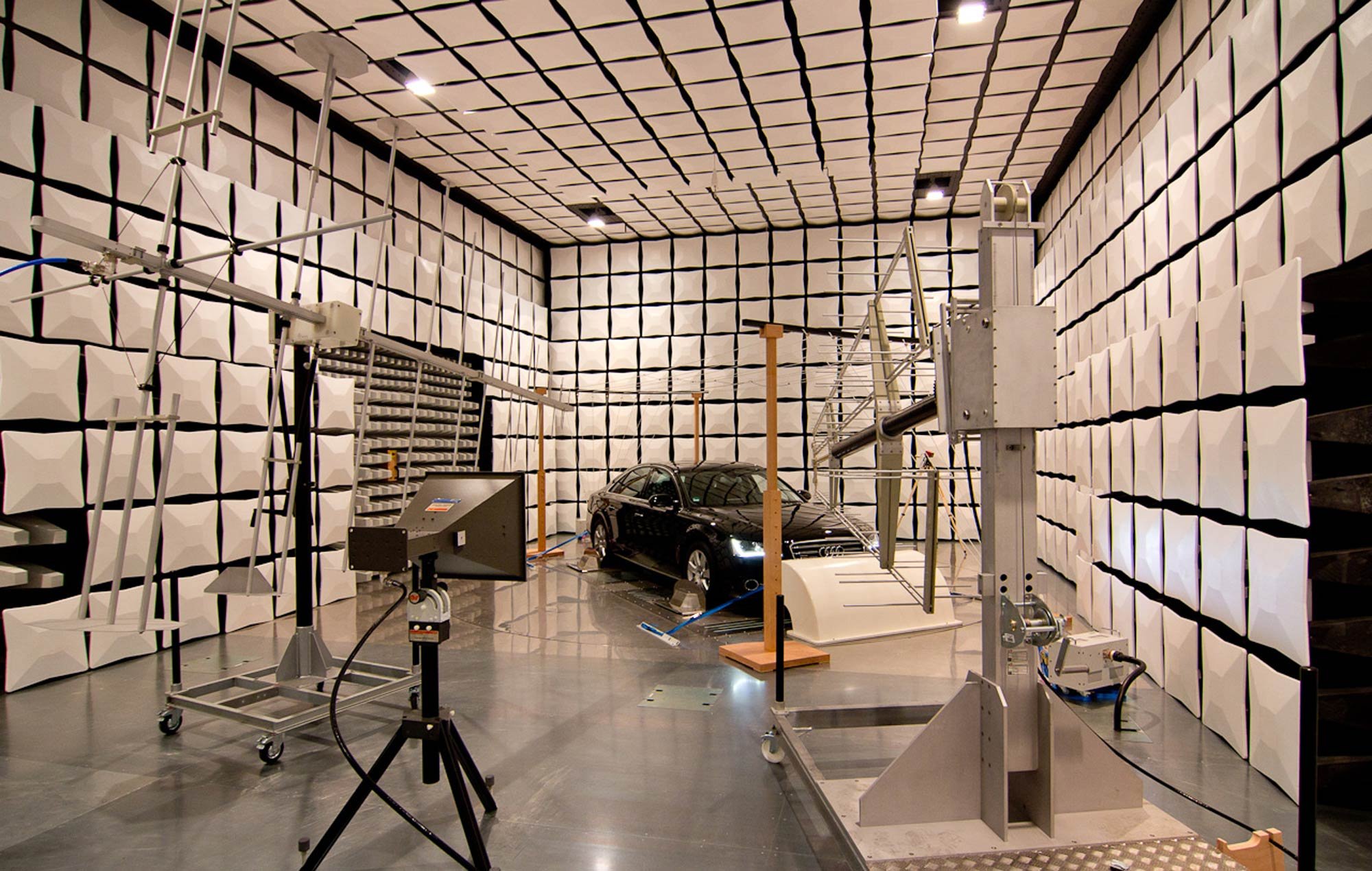
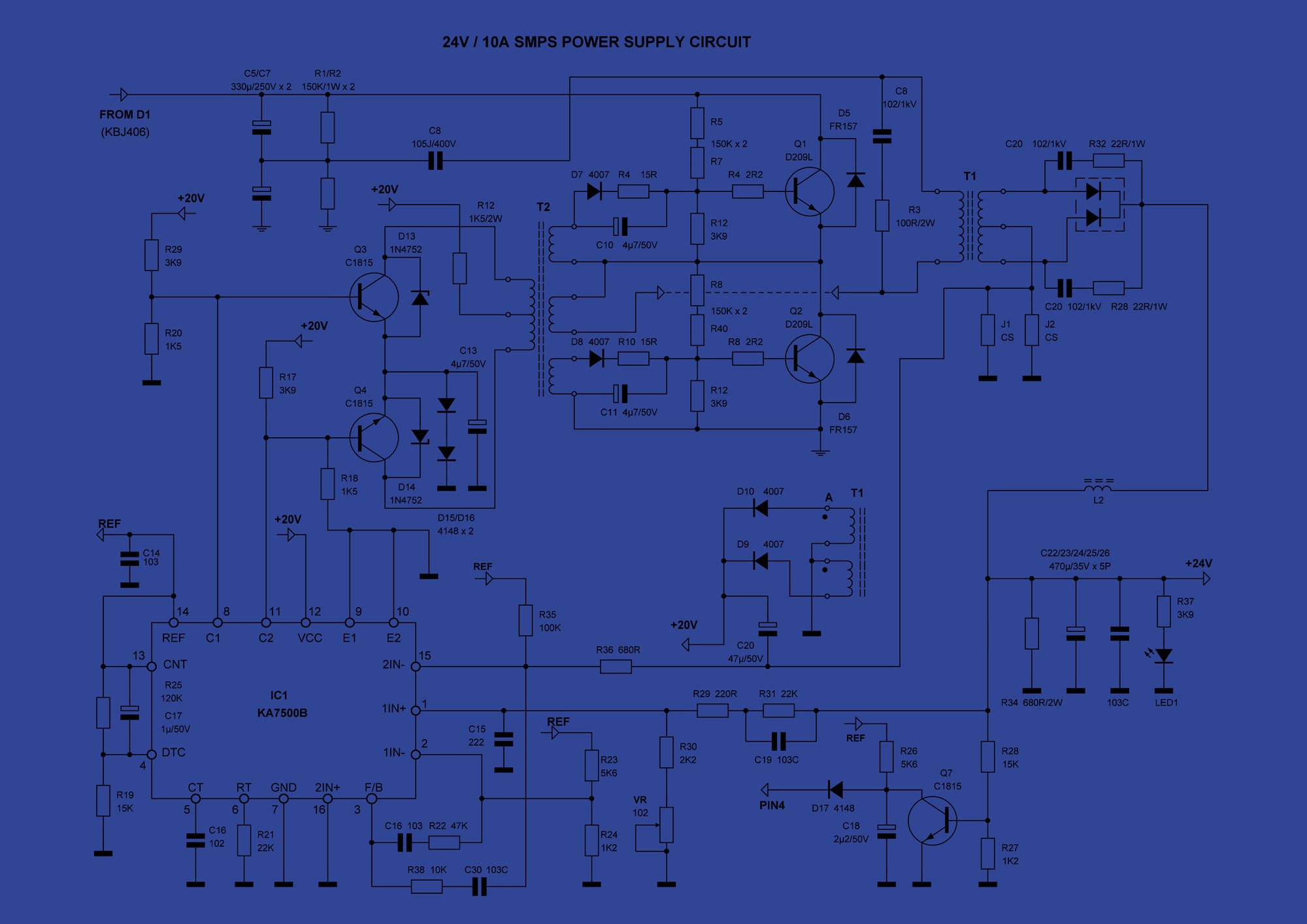
Start Here:
BCI Testing: MIL-STD-461 CS114, RTCA DO160 Sec 20, and ISO 11452-4
Bulk Current Injection (BCI) testing is one of the best ways to ensure that operations will not be interrupted by low frequency noise via either radiated or crosstalk mechanisms of interference.
All Bulk Current Injection (BCI) tests are addressing the same risk: given a relatively long cable run mounted relatively close to conductive structure (vehicle chassis), the cabling can pick up electromagnetic noise from the surrounding environment. Cabling is especially good at doing this at lower frequencies, below 200-ish MHz. Various sources can be: crosstalk from co-routed cabling, noise from on-board RF transmitters, or noise from the external environment (radars, comms, HIRF, etc.). At higher frequencies, the risk is addressed by testing radiated susceptibility/immunity (e.g. RS103) in a semi-anechoic or reverb chamber. However there are drawbacks to that approach at lower frequencies: the longer distances of radiated testing doesn’t represent the crosstalk risk; reverb chambers are harder to spec at lower frequencies; radiated testing at 1 m is in the near field at lower frequencies, which can lead to a lack of replicability. Additionally, BCI testing can be done in a shield room instead of a more specialized (and often harder to schedule) ALSE or reverb chamber.
Thus BCI testing, where current is directly induced in the cable under test (CUT), is generally preferable below 200 MHz. There are three comparable standards that do this for defense, aerospace, and automotive industries that are worth examining:
MIL-STD-461G, CS114 (Defense and aerospace)
RTCA DO160, Section 20 (Civilian aircraft)
ISO 11452-4 (Automotive)
Differences between the three can be seen immediately from their frequency ranges and maximum induced current levels:
CS114: 10 kHz - 200 MHz, up to 109 dBuA
DO160: 10 kHz - 400 MHz, up to 109 dBuA
ISO 11452-4: 1 MHz - 400 MHz, up to 100 dBuA
DO160 mentions specifically that their frequency range is meant to overlap with their radiated susceptibility testing range, which starts at 100 MHz. ISO, focused on the automotive industry, doesn’t have as many strong threats in the kHz range (although given the increasing prevalence of HV systems in EVs switching in the kHz range, I wonder if this will change in the future).
Another thing to compare is the maximum amplitudes. MIL-STD-461G has a good rule of thumb that for wiring suspended 5 cm above a ground plane (as is specified in all the test testups), an incident E-field of 1 V/m will result in 1.5 mA of induced current. CS114 and DO160 have maximum levels of 109 dBuA, equivalent to 300 mA and assuming a maximum threat of 200 V/m. In both cases, HIRF (high intensity radiated field) is one of the driving concerns. If we apply the same formula to ISO 11452-4, we get an incident field of 67 V/m. This is a bit odd because the maximum vehicle level radiated immunity test in this frequency range goes up to 100 V/m, but there may be a presumption that the vehicle chassis provides some level of shielding to the unit.
The other thing to consider is the modulation of the injected current and the dwell times. All methods recommend dwelling for the response time of the unit under test (UUT) but have different minimums:
CS114: Amplitude modulated (AM) only, dwell time 3 sec
DO160: Both AM and continuous wave (CW), dwell time 1 sec
ISO 11452-4: Both AM and CW, dwell time 1 sec
Generally speaking a unit tested to DO160 BCI would be considered equivalent to one tested to CS114, but the different dwell times means there’s a small chance the DO160 test could miss something, while the fact that CS114 doesn’t cover 200 - 400 MHz means there’s a small chance something could be missed there.
In other respects, the test setups between the three are generally identical. They all have cables suspended 5 cm above a ground plane, with a monitor probe in addition to the injection probe during testing. They test cable bundles per connector, and if it is known that chassis will be used for current return the ground lead is excluded from the cable bundle. For CS114 and DO160, if there are cables with redundant purposes they should all be subjected to the BCI stimulus simultaneously; this situation generally does not arise on automotive modules.
TIP:
To save time and hassle later, test all cables unshielded but have a shielded version ready to swap in if there’s a serious failure. Especially on aerospace projects it is not uncommon to spec that all cables will be shielded and to do EMC testing that way–then later in the project to ditch the shielding for cost/weight purposes, rendering the earlier EMC testing meaningless. Testing without shielding gives you good confidence that the unit will be OK if shields are removed, or it will give you hard data to show that shields are necessary.
TIP:
GSFC-STD-7000b (as usual) has some excellent additional information on this test method in Section 2.5.3.3.6, which expands on some fundamental aspects beyond what you’ll find in the MIL-STD-461 appendices.
ESD: IEC 61000-4-2, MIL-STD-461 CS118, ISO 10605, et. al.
Several standards cover ESD testing in similar ways. This article gives an overview plus places to look for additional guidance and alternate discharge models.
The basis for most ESD (electrostatic discharge) tests comes from IEC 61000-4-2, “Testing and measurement techniques–Electrostatic discharge immunity test”. The active 2008 version can be purchased here, with a new version expected in 2025. ISO 10605, “Road vehicles — Test methods for electrical disturbances from electrostatic discharge” (purchase 2023 version here) adopted the test method for the automotive industry. MIL-STD-461 included ESD testing for the first time with Rev G (freely available here) with the CS118 test method–and it looked pretty familiar. See comparisons below.
TIP:
If you have questions about ISO10605 or IEC 61000-4-2, you can see if there are answers in the freely available MIL-STD-461G CS118 or related appendix (Section A.5.16) before purchasing from IEC or ISO.
Testing is specified for units that are powered off (representing the danger from discharge when being handled or installed) and when turned on (representing threats present in its operating environment). They also include air and contact discharge, with air discharge generally being more severe. Contact discharge is mating two conductive objects at different potentials together and seeing the surge of charge transfer. Air discharge is when you reach for a metal doorknob on a dry/cold day and feel an actual spark just before you touch the door. Maximum testing voltages should be adjusted based on the expected operating conditions (how often humans interact with the unit, if it is installed in a humidity-controlled environment, etc.).
TIP:
ANSI C63.16, “Guide for Electrostatic Discharge Test Methodologies and Acceptance Criteria for Electronic Equipment”, is an available guidance document for ESD testing (the 2016 version is available for purchase here; a new version has been drafted and is currently going through ANSI approvals). It gives additional context
Almost all ESD test standards and commercially available ESD test guns/simulators base their waveforms off the human body model (HBM). The CS118 version is below.
However, there are cases where the main threat does not come from human interaction. Generally speaking the industries have determined that testing based on the HBM is adequate to identify most hardware weaknesses to ESD (although the ANSI C63.16 working group will tell that’s definitely not 100% true). I was once looking into a case where the main threat to a satellite orbiting in Low Earth Orbit was definitely going to be spacecraft charging, and did some research to see if there were other standard models available.
TIP:
The only one I was able to find was from an outdated military standard, MIL-STD-1541A (1987) (freely available here). You can see an alternate discharge model below, and the document has information about ways to vary different parts of the circuit to address different threat waveforms.
MIL-STD-331D (download here) includes circuit values for helicopter-based discharges for fuzing systems and ignition protection devices as well, to be inserted into a more traditional IEC 61000-4-2 circuit setup. Appendix A.5.8.3.2 of MIL-STD-464D also has information on helicopter-borne discharges & ordnance.
ISO 7637: “Road vehicles — Electrical disturbances from conduction and coupling”
ISO 7637 is the automotive standard that sets out test methods for evaluating conducted immunity at the module level.
ISO 7637 defines test methods for determining how modules react to transient disturbances (conducted immunity).. ISO 7637-1 sets out general principles and can be purchased and downloaded from the ISO. It has four separate parts, with parts 2, 3, and 4 outlining specific test methods. A summary of what is in each part is included below.
For a given electronics module that draws typical 12V power, testing to both ISO 7637-2 and -3 will likely be needed. For units that interface with shielded high voltage power lines in an electric vehicle, ISO 7637-4 will apply. There are a lot of transients associated with operating a car/bus/truck–power surges on startup, transients from large inductive loads (motors) switching on and off, transient interruptions as connections are jostled loose by the bouncing of the car over roads for multiple years, etc. Testing for conducted immunity can be a significant portion of your overall EMC testing schedule.
ISO 7637 shares with ISO 11451 the structure of evaluating unit performance based on a functional performance status classification system, which is useful even outside the automotive industry.
ISO 11451: “Road vehicles — Vehicle test methods for electrical disturbances from narrowband radiated electromagnetic energy”
ISO 11451 is a collection of test methods addressing vehicle level immunity to electric fields.
ISO 11451 is a collection of documents that describe automotive test methods for testing at the vehicle level to show immunity to various levels of electromagnetic environment. You can purchase 11451-1 here, and the same site has the other parts available as well. The parts are all revised on their own schedules, with Part 1 (current version published in 2015) expected to have a new revision published in 2024.
ISO 11451 is applicable to any kind of passenger car or commercial vehicle, whether traditional internal combustion engine or electric. Its test methods cover the frequency range 10 kHz - 18 GHz, but it is more often applied within a narrower range, such as 1 MHz - 2 GHz. Table 1 lists the different test methods available.
*LUF = lowest usable frequency of a particular reverb chamber.
TIP:
Remember that the plane wave illumination at each frequency in ISO 11451 testing isn’t a constant continuous wave. Different modulations are applied to different frequency ranges to better capture real world threats.
TIP:
ISO 11451 defines a set of functional performance status classifications (seen below). Widely used in the automotive industry, these categories can be helpful in defining the success criteria for immunity/susceptibility testing for many complex systems, either at the platform or module level. When a device under test has many functions, some of them may be more critical than others. For instance, if the infotainment system gets knocked offline, that’s inconvenient for the user, and the manufacturer may want to address the issue if it happens at too low of a field strength, such that it might happen often. On the other hand, if the headlights can get turned off by any of the test exposures, that would be a major safety concern that would have to be addressed. Combining the criticality of different functions with the performance status classifications from ISO 11451 in a test plan can be a good way to predetermine which “failures” or “anomalies” are acceptable and which must be labeled failures and fixed. It’s a more detailed framework than the “must function normally” criteria found within some immunity/susceptibility test plans.
ISO 11452: “Road vehicles — Component test methods for electrical disturbances from narrowband radiated electromagnetic energy”
ISO 11452 is a standard with multiple parts and test methods that covers testing components that will go on vehicles (cars, trucks, etc.) for immunity.
ISO 11452 covers automotive components for immunity testing--with, as we see with several other standards, a whole lot of parts that can be bought separately. You can see which parts cover which test methods in the tables below. You can start by looking at ISO 11452-1 (“General principles and terminology”) which is available for purchase here. The current version is from 2015 and a new revision is expected in the next year or so.
ISO 11452 uses CISPR 16 to govern the measurements equipment used. Annex A of ISO 11452-1 has a very useful normative guide on how to classify the performance of different functions during testing (you would not call a test a failure if an infotainment system spontaneously reset during moderate level testing; the brake system doing the same thing would be considered a critical failure).
You might notice similarities between ISO 11452 and its various parts and those of SAE J1113. That’s not a coincidence--J1113 was essentially the North American version of the same document until they came into agreement.
TIP:
If you have the facility available, testing in a reverb chamber (ISO 11452-11) is often the fastest way to test and also the one most likely to find problems. That sounds like a bad thing, but it’s much better to find problems when it’s one component in a chamber instead of troubleshooting an entire vehicle.